The trend to limit the use of plastics is balanced by recycling and lightweighting, concepts that drive the production of machines
The trend to limit the use of plastics is balanced by recycling and lightweighting, concepts that drive the production of machines. These require state-of-the-art components to be efficient: particularly in the extrusion segment, which is a cost effective transformation process, it is essential to take into account materials, components and support equipment to optimize performance and product quality.
Circular economy and energy efficiency
The tendency to limit the use of plastics in certain sectors has inevitably influenced the market trend for machines for the production of objects made of this material. But new growth opportunities for the sector come from circular economy and the fight against polluting emissions.
Although the development of the sector has slowed down in the last two years, this has occurred after a long period of growth, during which the industry strengthened allowing companies to invest in research and development of new technologies.
The very current theme of circular economy represents for the entire sector an opportunity for considerable development, provided that the industries propose plants in an Industry 4.0 perspective, with production cycles based on energy saving and the ability to reprocess recycled plastics.
Such machinery will require cutting-edge components.
R+W Italia is well aware of this, and already has products in its catalogue able to meet the needs of manufacturing companies. Machinery for plastic recycling can in fact reach maximum efficiency if equipped with cutting-edge devices such as torque limiters, able to prevent machine downtime by coming into operation when an overload should block the plant. Without torque limiters the risk of failure or breakage is very high; similar accidents can stop the entire production and affect the competitiveness of the company.
Zero emissions for cars can also be a chance: the increasingly stringent limits on emissions of nitrogen oxides, hydrocarbons, particulate matter, carbon monoxide and, more recently, even CO2 imposed by the EU on cars will boost the use of plastics in the automotive sector. Actually, plastic is the ideal material for reducing the weight of cars, which translates into lower consumption and less polluting emissions.
Among the plastics processing technologies, extrusion is of particular interest, aimed at the production of finished products for industry or for applications dedicated to the final consumer: it is a process characterised by high levels of integration.
This property means that the implementation of this process can open up two typical scenarios:
- the extruder is a component of the production line;
- the extruder makes up the entire production line.
Among the main critical points of the process is, for example, the optimal temperature control of the extruder. Incorrect temperature regulation would, in fact, lead to the inappropriate formation of the polymeric compounds used, inefficient cooling of the feeder, incorrect melting temperature at the extruder outlet, the extractor at the end of the production line being operated at the wrong speed or any other incorrect operating condition in combination with the others.
In addition to the activity of setting the production parameters, there is also the programming all the ordinary and extraordinary maintenance operations. These activities will turn out to be optimal in the management of a production line, where a correctly designed plastic extruder operates. For such a machine, the optimal choice of the drive components by the designer is a determining factor for the achievement of both the pre-established productivity levels and the quality of the final product.
The choice of components is also fundamental in achieving the appropriate performance levels of the plant, in terms of synchronism of the timing of the individual production phases, in order to further ensure product conformity.
Figure 1 shows the functional scheme of a plastic extrusion plant.
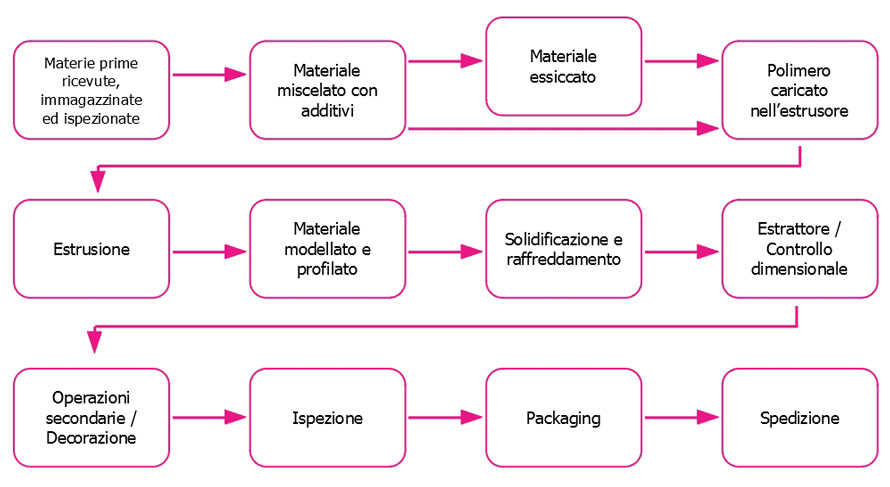
The molten material is subsequently forced through the opening of the die plate. The resulting profile is then cooled down: further passages of the profile are possible through a series of dimensioning plates or forming tools, in order to obtain the final shape of the product section.
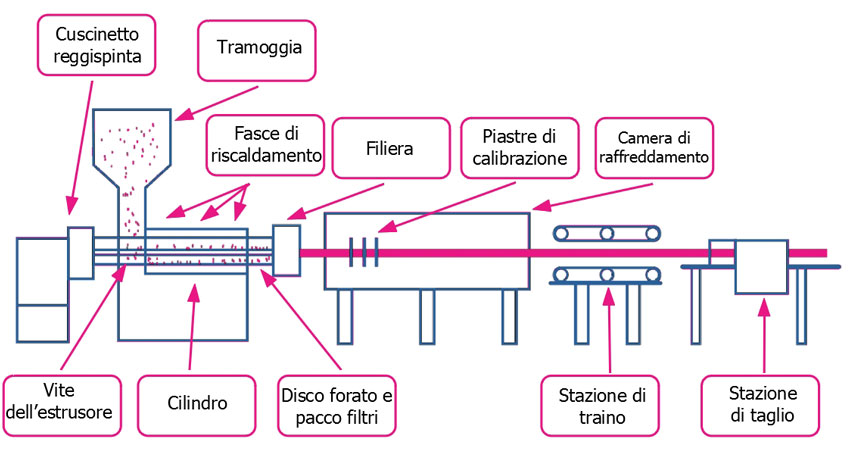
The excess heat from the profile is then removed by means of cold water baths, compressed air jets or contacts with cooling surfaces, in order to achieve the appropriate levels of dimensional stability before the final stages of production.
Components and functionality of a plastic extruder
The components of an extruder can be schematically represented as in Figure 2; this schematization is valid both when the extruder is a single machine and when it makes up the entire production line.
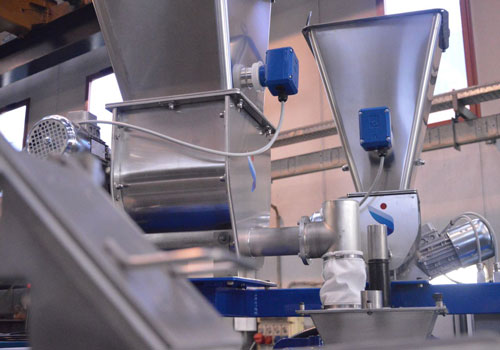
Consider the system shown in Figure 3.
The main task of the cylinder is to house the screw and to provide the development path to the die for the production of the desired profile. Consider the system shown in Figure 4.
The design of the extruder screw is such as to allow the subsequent dosing and gradual melting of the plastic material pellets; at the same time, the screw exerts pressure on the material with consequent stress along its axis. During the rotation of the screw, the resin pellet is subsequently dosed by its threads and gradually melted, developing pressure along its path.
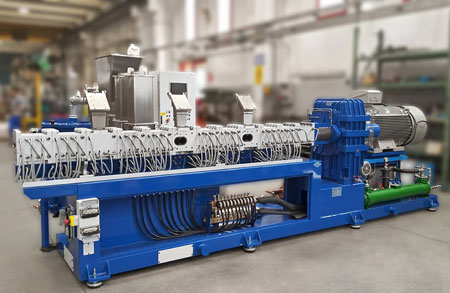
The design of this component requires, however, further investigation and preliminary investigations during research and development activities.
In order to face the evident design issues of an extruder screw, numerical simulation techniques based on Computational Fluid Dynamics (CFD), Finite Element Method (FEM) and Discrete Element Method (DEM) are used. The use of CAE software implementing these simulation techniques, facilitates the reliability of design and prediction of operating conditions.
Figure 5 shows the results of a transient multi-phase simulation of mixture distribution quality. This type of simulation integrates, for example, the results of the biphasic transient simulation shown in Figure 6, which allow the calculation of partially filled screw sections according to the Design of Experiment (DOE) prerogatives.
The evident complexity of the use of such simulation techniques is further increased when the contribution of flow heat and pressure, both increasing as the material reaches the die, are considered. These factors are crucial in the design of twin-screw extruders, as shown in the simulation results in Figure 7.
The thrust bearing sizing considers its positioning between the screw and the assembly given by the kinematic coupling between motor and gearbox. It is thus subject to the axial load resulting from the screw rotating against the plastic material being processed. This prevents backward movement of the screw in the cylinder, absorbing the loads generated by the screw during the process. Figure 8 shows the detail of the thrust bearing inside an extruder gearmotor unit.
The heating bands keep the temperature of the material constant in a certain area of the cylinder.
An example of a heating band is shown in Figure 9.
The purpose of the perforated disc is to hold the filter pack in its housing. An example is shown in Figure 10.
The filter pack consists of a series of wire filters in the form of nets of different sizes, used to filter out any contaminants or unmelted resin particles before they reach the die, protecting it from damage.
Figure 11 shows an overview of the type of filters commonly produced.
The purpose of the die is to ensure that the heated material takes the required shape. In plastic extrusion plants, the most common types of dies are standard flat and conical. Figure 12 shows an example of a die for the production of technical profiles.
In the cooling chamber, the profile passes through a moving water bath or through a series of compressed air jets. This component may be equipped with reshaping systems to maintain allowance and shape retention requirements. Figure 13 shows a water bath cooling chamber with a proprietary extrusion anti-ovalization system.
Figure 14 shows a set of calibration plates with the cooling system.
At the exit of the cooling chamber, the profile enters a towing station. This component is responsible for keeping the profile moving through the entire process at a constant speed. An example of a towing station is shown in Figure 15.
The profile thus reaches the cutting station, which is now completely cooled down. Figure 16 shows an example of a cutting station.
The role of the component supplier
The design of a plastics extrusion plant requires a careful choice of kinematic couplings. R+W, a leading manufacturer of couplings and line shafts, offers its experience to the designer. In all those extruders where it is necessary to combine kinematic chain protection and vibration dampening requirements, R+W also provides a complete range of solutions for all transmission requirements such as ST series torque limiters.
Absolutely backlash-free, ST torque limiters allow the motor system to be protected in case of overload, disconnecting it from the driven part within milliseconds. Extremely accurate, they transmit torque with great accuracy and take action only when necessary. They also allow quick and easy re-setting as soon as the cause of the overload is removed.
For personalised advice, contact R+W by phone (+39 02 2626 4163), via e-mail (info@rw-italia.it), via webchat available at www.rw-giunti.it or via the company’s social channels.
Nuove opportunità di crescita per l’estrusione della plastica
La tendenza a limitare l’uso della plastica è bilanciata da riciclo e alleggerimento, concetti cheforniscono nuovo impulso alla produzione di macchinari
La tendenza a limitare l’uso della plastica è bilanciata da riciclo e alleggerimento, concetti che forniscono nuovo impulso alla produzione di macchinari. Questi richiedono componenti all’avanguardia per essere efficienti: in particolare nel segmento dell’estrusione, processo di trasformazione economicamente conveniente, è fondamentale tener conto di materiali, componenti e attrezzature di supporto per ottimizzare prestazioni e qualità dei prodotti.
Economia circolare ed efficienza energetica
La tendenza a limitare l’uso della plastica in alcuni settori ha inevitabilmente influenzato l’andamento del mercato delle macchine destinate alla produzione di oggetti in questo materiale. Ma nuove opportunità di crescita per il settore arrivano dall’economia circolare e dalla lotta alle emissioni inquinanti.
Sebbene lo sviluppo del settore abbia conosciuto un rallentamento negli ultimi due anni, questo si è verificato dopo un lungo periodo di crescita, durante il quale il comparto si è rafforzato consentendo alle imprese di investire nella ricerca e nello sviluppo di nuove tecnologie.
L’attualissimo tema della circular economy rappresenta per l’intero comparto un’opportunità per un notevole sviluppo, a condizione che le industrie propongano impianti in chiave Industry 4.0, con cicli produttivi improntati al risparmio energetico e capacità di riprocessare materie plastiche riciclate. Macchinari che richiederanno una componentistica all’avanguardia.
Lo sa bene R+W Italia, che già ha in catalogo prodotti capaci di rispondere alle esigenze delle aziende produttrici. I macchinari per il riciclaggio della plastica possono infatti raggiungere la massima efficienza se dotati di dispositivi all’avanguardia come limitatori di coppia capaci di prevenire i fermi macchina entrando in funzione nel momento in cui un sovraccarico di lavoro dovesse bloccare l’impianto. Senza i limitatori di coppia il rischio di registrare guasti o rotture è molto elevato; incidenti simili possono fermare l’intera produzione e inficiare la competitività dell’azienda.
Anche le emissioni zero per le auto possono essere una chance: i limiti sempre più stringenti alle emissioni di ossidi di azoto, idrocarburi, polveri sottili, monossido di carbonio e, più recentemente, anche di CO2 imposti dalla UE alle automobili daranno impulso all’utilizzo delle materie plastiche nel settore automotive. La plastica rappresenta infatti il materiale ideale per la diminuzione del peso delle vetture, che si traduce in minori consumi e meno emissioni inquinanti.
Il processo di estrusione plastica
Fra le tecnologie di trasformazione delle materie plastiche riveste particolare interesse l’estrusione, finalizzata alla produzione di prodotti finiti destinati all’industria o ad applicazioni dedicate al consumatore finale: si tratta di un processo caratterizzato da alti livelli di integrazione.
Tale caratteristica fa sì che l’implementazione di tale processo possa aprire a due scenari tipici:
- l’estrusore costituisce un componente della linea di produzione;
- l’estrusore costituisce l’intera linea di produzione.
Tra le principali criticità del processo vi è, ad esempio, la regolazione ottimale della temperatura dell’estrusore. Una scorretta regolazione della temperatura determinerebbe, infatti, la formazione non appropriata delle mescole polimeriche impiegate, il raffreddamento non efficiente della gola di alimentazione, la temperatura di fusione errata all’uscita dell’estrusore, l’estrattore alla fine della linea di produzione che viene azionato non alla giusta velocità o una qualsiasi altra condizione operativa scorretta in combinazione con le altre.
All’attività di settaggio dei parametri di produzione, va poi affiancata quella di programmazione di tutti gli interventi di manutenzione ordinaria e straordinaria. Tali attività risulteranno ottimali nella gestione di una linea di produzione, all’interno della quale opera un estrusore plastico correttamente progettato. Per tale macchinario, la scelta ottimale dei componenti degli azionamenti da parte del progettista, costituisce un fattore determinante per il conseguimento sia dei livelli di produttività prestabiliti che della qualità del prodotto finale.
Tale attività di scelta dei componenti è fondamentale anche nel conseguimento degli opportuni livelli prestazionali dell’impianto, in termini di sincronismo dei tempi di esecuzione delle singole fasi di produzione, al fine di garantire ulteriormente la conformità del prodotto.
Nella Figura 1 viene mostrato lo schema funzionale di un impianto di estrusione plastica.
Il materiale fuso viene forzato successivamente attraverso l’orifizio della piastra della filiera. Il profilo così ottenuto viene successivamente sottoposto a raffreddamento: ulteriori passaggi del profilato sono possibili attraverso una serie di piastre di dimensionamento o di utensili di formatura, al fine di ottenere la forma finale della sezione del prodotto.
Il calore in eccesso dal profilo viene poi rimosso tramite bagni di acqua fredda, getti di aria compressa o contatti con superfici raffreddanti, al fine di conseguire gli opportuni livelli di stabilità dimensionale prima delle fasi finali di produzione.
Componenti e funzionalità di un estrusore di materie plastiche
Le componenti di un estrusore possono essere schematicamente rappresentate come in Figura 2; tale schematizzazione è valida sia nel caso in cui l’estrusore costituisca un macchinario singolo, che in quello in cui sia rappresentativo dell’intera linea di produzione.
Si consideri il sistema mostrato in Figura 3.
Compito principale del cilindro è quello di ospitare la vite e di fornire il percorso di sviluppo alla filiera per la produzione del profilo desiderato. Si consideri il sistema mostrato in Figura 4.
La progettazione della vite dell’estrusore è tale da consentire il dosaggio successivo e la fusione graduale del pellet di materiale plastico; contestualmente a tali azioni, la vite esercita una pressione sul materiale con conseguente sollecitazione lungo il suo asse. Durante la rotazione della vite, il pellet di resina viene successivamente dosato dai suoi filetti e gradatamente fuso, sviluppando pressione lungo il suo percorso.
La progettazione di tale componente richiede, comunque, ulteriori approfondimenti ed indagini preliminari durante le attività di ricerca e sviluppo.
Per affrontare le evidenti le criticità progettuali della vite di un estrusore, si ricorre a tecniche di simulazione numerica basate sulla Fluidodinamica Computazionale (CFD), sul Metodo degli Elementi Finiti (FEM) e sul Metodo degli Elementi Discreti (DEM). L’impiego di software CAE che implementano tali tecniche di simulazione, agevola l’affidabilità delle attività di progettazione e di predizione delle condizioni operative
Nella Figura 5 vengono mostrati i risultati di una simulazione multifase in regime transitorio della qualità di distribuzione della miscela. Tale tipo di simulazione integra, ad esempio, i risultati della simulazione in regime transitorio bifasica mostrata in Figura 6, che permettono il calcolo delle sezioni della vite riempite parzialmente secondo le prerogative del Design of Experiment (DOE).
L’evidente complessità dell’impiego di tali tecniche di simulazione viene ulteriormente incrementata quando si tiene conto del contributo del calore da scorrimento e della pressione, entrambi crescenti fino al raggiungimento della filiera da parte del materiale. Tali fattori risultano determinanti nella progettazione degli estrusori bivite, come mostrato nei risultati della simulazione in Figura 7.
Il dimensionamento del cuscinetto reggispinta tiene contro del suo posizionamento tra la vite ed il gruppo dato dall’accoppiamento cinematico tra motore e riduttore. Esso risulta così soggetto al carico assiale derivante dalla vite posta in rotazione contro il materiale plastico in lavorazione. Previene così il moto retrogrado della vite nel cilindro, assorbendo i carichi generati dalla vite durante il processo. In Figura 8 viene mostrato il particolare del cuscinetto reggispinta all’interno di un gruppo motoriduttore di un estrusore.
Le fasce di riscaldamento hanno il compito di mantenere costante, in una certa zona del cilindro, la temperatura del materiale.
In Figura 9 viene mostrato un esempio di fascia di riscaldamento.
Compito del disco forato è quello di ritenere il pacco filtri nel suo alloggiamento. In Figura 10 ne viene mostrato un esempio.
Il pacco filtri consiste in una serie di filtri in filo metallico sotto forma di retine di diverse dimensioni, usato per filtrare gli eventuali contaminanti o particelle di resina non fusa prima che essi raggiungano la filiera, proteggendola dal danneggiamento.
In Figura 11 viene mostrata una rassegna della tipologia di filtri comunemente prodotti.
Il compito della filiera è quello di far sì che il materiale riscaldato assuma la forma richiesta. Negli impianti di estrusione delle materie plastiche, le tipologie di filiere più ricorrenti sono quella piana standard e quella conica. In Figura 12 viene mostrato un esempio di filiera per la realizzazione di profili tecnici.
Nella camera di raffreddamento, il profilo passa attraverso un bagno d’acqua in movimento o attraversi un serie di getti di aria compressa. Tale componente può essere dotato di sistemi di rimodellamento per il mantenimento dei requisiti di tolleranza e di conservazione della forma. Nella Figura 13 viene mostrata una camera di raffreddamento a bagno d’acqua con sistema proprietario di antiovalizzazione dell’estruso.
In Figura 14 viene mostrato un set di piastre di calibrazione con relativo il sistema di raffreddamento.
All’uscita della camera di raffreddamento, il profilato fa il suo ingresso in una stazione di traino. Tale componente il compito di mantenere il profilo in movimento attraverso l’intero processo, ad una velocità costante. In Figura 15 viene mostrato un esempio di stazione di traino.
Il profilo raggiunge così la stazione di taglio ormai completamente raffreddato. In Figura 16 viene mostrato un esempio di stazione di taglio.
Il ruolo del fornitore di componenti
La progettazione di un impianto di estrusione di materie plastiche richiede una scelta accurata degli accoppiamenti cinematici. R+W, azienda leader nella produzione di giunti e alberi di trasmissione, è in grado di mettere la sua esperienza a disposizione del progettista. In tutti quegli estrusori in cui è necessario combinare le esigenze di protezione della catena cinematica a quelle di smorzamento delle vibrazioni, R+W fornisce anche una gamma completa di soluzioni per tutte le esigenze di trasmissione quali i limitatori di coppia della serie ST.
Assolutamente privi di gioco, i limitatori di coppia ST permettono di proteggere il sistema motore in caso di sovraccarico, scollegandolo dalla parte condotta nel giro di pochi millisecondi. Estremamente precisi, trasmettono la coppia con gande accuratezza e intervengono solo in caso di effettiva necessità. Inoltre consentono un riarmo semplice e rapido non appena viene rimossa la causa del sovraccarico.
Per una consulenza personalizzata, contattate R+W telefonicamente (02 2626 4163), via mail (info@rw-italia.it), tramite webchat disponibile sul sito www.rw-giunti.it o tramite i canali social dell’azienda: potrete contare su #progettiSicuri con R+W!