FAP’s evolution towards a complete customer service model, continuously updated through unparalleled R&D efforts
Through its clients, FAP has historically responded to the most current needs in the construction, packaging, and automotive sectors. Founded by Luigi Poli in 1987 and now led by his sons Fabrizio and Francesco, the company manufactures extrusion lines for foam, automatic winders, laminating lines, and other tailored made converting machinery, alongside all modern connected services, from preventive maintenance to personnel training and support.
“We’ve gone beyond the classic customer service, diving into consulting and project support for entrepreneurs looking to build a new production facility or start producing a new material,” explains Francesco Poli, CEO and Sales Director of FAP. “Not only can we offer insight into the type and number of machines needed, but also handle all aspects of managing the production facility, from space requirements to personnel shifts.”
The expansion of services, with a strong emphasis on R&D, is one of the innovations introduced by the Poli brothers when they took over the family business in 2020. “We’ve made significant investments in the new production area and created new services to offer our clients a comprehensive solution,” says Francesco Poli. “The starting point was recognizing the growing difficulty companies face in finding qualified personnel, so we took action to support our clients in this area as well.”
FAP’s target market ranges from large multinationals to small family-owned businesses, mostly international clients, particularly in Europe, as well as in North and South America. “When we design a machine, we always consider the investor’s perspective—this has always been our approach and something we’re recognized for. The current scenario pushes us to create machines that are increasingly automated and easy to use, addressing labor shortages. Other key trends are green design, speed, flexibility, and project customization.”
FAP is guided by the principles of the ESG philosophy, aiming to minimize the energy consumption of its new machinery. These energy-intensive systems benefit from every optimization, positively impacting company costs. For example, to reduce energy consumption during start-up, FAP has equipped its machines with software that manages the heating process to avoid energy spikes, achieving the same result by modulating energy demands. Each machine is customized to client requests, minimizing delivery and setup times.
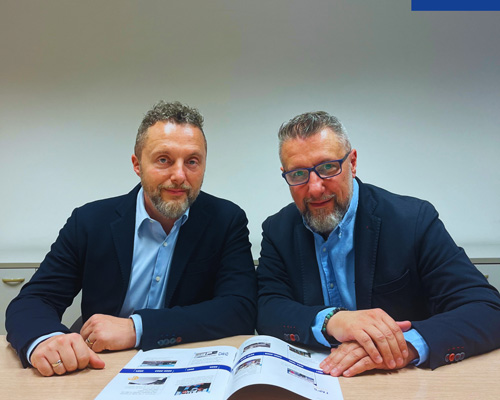
Sustainability remains a major focus of FAP’s ongoing research: “For about 10 years, we’ve been working in collaboration with a major university in Milan on a system for producing foam using CO2, an alternative gas to isobutane, derived from petroleum, which is generally used,” continues Francesco Poli. “To date, we have obtained the first two patents, both Italian and European, in anticipation of future applications in two new sectors for us, the food and pharmaceutical industries.”
The R&D department is crucial for FAP, which is also why the company chose to expand and renew its facility in Besana in Brianza. “Historically, we’ve collaborated with the leading plastic producers to develop new materials, giving them the ability to conduct industrial tests. The new facility, which will be completed in 2025, will not only expand the production space dedicated to FAP but will also feature a separate laboratory area expressly dedicated to research, development, and a showroom.” A new frontier to keep FAP at the forefront of the innovation race.